Bushcraft axe making – Part 1 – metal working.
How to make bushcraft axes tutorial using repurposed steel. Series on bushcraft axe making on how to make a full tang high carbon steel survival axe. This axe making tutorial will take you through the steps of making two axes from start to finish. A plow disk will be used to make the axes because this metal is high carbon steel and will take the abuse and stand up to the test in the field. The plow disk I will be using for this project is 3/16″ thick and is a sod disk you can find thicker disk and they are called rock disc and are used where there are a lot of rocks in the field being plowed. The thickness of the rock disk is 1/4″ and is equal to O1 steel or 1095 as far as carbon content and is just perfect for making bushcraft axes with full tangs.
If you like the axe making video please check the like button. If you watch all four parts of the series I think you will like what you see.
This is a light weight axe that is perfect for bush crafting it’s not the only axe you will need but a good lightweight ax for hiking a long way and not being weighted down by heavy gear.
Thanks for taking your time to watch this axe making tutorial.
Bushcraft axe making – Part 2 – metal working.
How to tutorial to make your own bushcraft axes using re purposed metal and steel. Once the handles are roughed out I use a 80 grit to grind down close to my pencil mark and then determine the right and left side of the handles and do some more pre-shaping and fitting and then set the handles aside for a while. It’s time to hammer the edge onto the axe face rather than the stock removal method. Also re inspect the the axe for straightness from tang to axe head and straighten if necessary to make sure the axe is straight before heat treating.
Bushcraft axe making – Part 3 – metal working.
Heat treating steel and fitting the Micarta handles on these handmade bushcraft axes.
Before I secure the handles I need to heat treat the axe, axes I start by belt sanding both sides with an 80 grit belt on my 2″ X 72″ belt grinder to remove the crust that developed when I hammered the cutting edge on the face of the axe and straightened the tang. As you can see my 2 X 72 belt sander/grinder is a homemade affair and it works great I have been using this for so long I can’t even remember what year it was put together. Axe making tutorial. I purchased the idler and contact wheels from a knife making supply house in Florida called Sheffield Knifemakers Supply, I have not purchased anything from them in along time because I am here in north Texas and I have a supplier a little closer to home so when I order grinding and polishing supplies I can usually have the order the next day or two.
Bushcraft axe making – Part 4 – metal working.
How to Make Bushcraft Axes – Tutorial Part 4 Finishing handmade bushcraft axes How to video tutorial. Handmade bushcraft axes are designed to be worn on you belt and will not weigh you down but don’t let that fool you these axes pack a powerful punch because they are sharp and made good steel.
Axe making start to finish with Bruce Cheaney. In this video clip it is time to heat treat the bushcraft axes I start off by heating the axes up in the propane forge and when they reach the proper temperature a non magnetic state, now it is time to quench the axe in oil. I use olive oil for quenching my knives and axes you can use motor oil and special quenching oils but I prefer olive oil because it works for me.
After the axe has been quench it is time to clean the oil off of the axe as well as the fire scale this can be done with a 120 and 320 grit sanding belt on the belt sander/grinder. Now it is time to temper the full tang axe I do this by preheating my kitchen stove to 450 degrees and putting the knives and axes in for one hour at 450 and then turn the stove off and let the blades and axes cool down slowly. The end result is what expected a very sharp piece of steel that holds a good edge under normal use.
You can find all kinds of steel to make your own Bushcraft Knife Blade out of like plow disc, crosscut saw blades, saw mill blades, car leaf springs, and even flat files. Yes you can buy Bushcraft Knives but there is much more pride in ownership if you hand make a knife yourself out of steel you can find laying around or in the scrap pile.
Bushcraft knife making with Bruce Cheaney Gainesville, Texas takes you through the steps of making a handmade bushcraft knife that can be used for bushcraft and hunting. This is a handmade knife that is made to be used in the wilderness and hunting or survival.
I purchase my knifemaking supplies from a supplier here in the central United States called Jantz Knife Making Supplies they stock just about anything a knife maker might need for making knives such as knife steel and handle material. You can also find enough parts to make your own belt grinder or purchase a Bader Grinder B-III , KMG Grinder from Beaumont Metal Works or Burr King Knifemaker Machine.
Bushcraft Knife Making Video
With just a little effort you can make your custom Bushcraft Knife Sheath out of saddle skirting or strap leather and either hand sew the sheath or lace it together with Indian tan lace leather or Kangaroo lace either one will work very good.
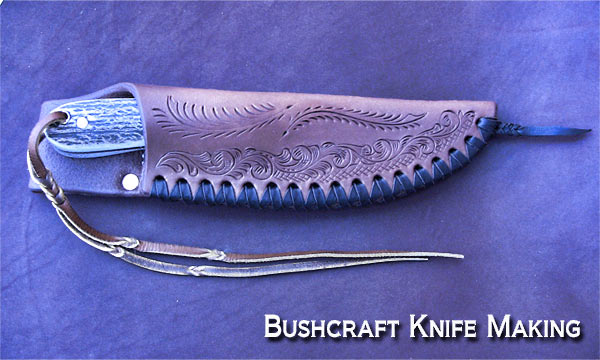
Bushcraft Knife Making
Knife making for beginners – High carbon steel black Micarta handle brass pins brass lanyard hole. Handmade from start to finish and made to be used. This is a totally handmade made from an old plow disk. The handle is made from Micarta and fastened with Corby fasteners and two handmade brass pins.
Making knives using belt sander, bench grinder, acetylene torch and anvil. Bushcraft making tutorial – Drilling tang holes. Drilling tang holes in bushcraft blanks. I start this making tutorial off by checking my drill bits that I will be using to drill the tang holes in the three bushcraft I have in the works. Next I will center punch my tang holes with a center punch and ball peen hammer. I use a small drill press made by Ryobi that is just the right size and is not to powerful that would cause problems if the drill bit gets hung up.
Bushcraft Knifemaking Tutorials – DIY – Bruce Cheaney How to videos – Knife Making for Beginners. Making with limited metal working tools. Profile your tool with a abrasive cut off wheel and a Baldor number 114 buffer motor.
Knife Making for Beginners – Bushcraft Knife Review – Handmade Bushcraft Knives and Axe. Series on bushcraft knife making review how the knives turned out after the tool handles were epoxied onto the tangs.
How to epoxy bushcraft knife handles with Gorilla Glue. Time to epoxy the Micarta handles onto my handmade bushcraft tool. The work is done the blade is made clean up and heat treated the Micarta tool handles have been pre-fitted and it is time to epoxy them onto the tang. I will be using Corby bolts for three fasteners and two brass handmade pins that I made out of brass welding rod and have flared them out on one side and cut them to the right length to be peened on the other side.
The epoxy I will be using on the bushcraft tool is made by The Gorilla Glue Company and it is their version of five minute epoxy. The thing I like about this five minute epoxy is that it is clear and has the ability to fill in slight cracks and spaces.
I made my own stirring sticks out of 1/16″ tig welding rod. My work area is prepped and ready I have cardboard to mix the epoxy on and Acetone to remove any excess epoxy once the handles are attached.